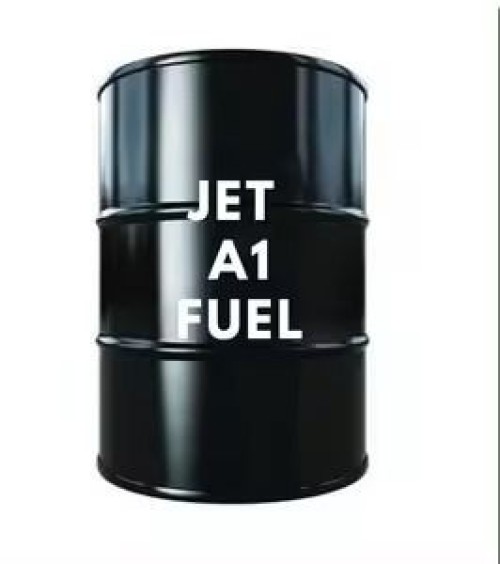
PROPERTY
LIMITS
IP
ASTM
REMARKS
TEST METHOD
APPEARANCE
Visual appearance
Clear, bright and visually free from solid matter and un-dissolved water at ambient fuel temperature
Colour
Report
D 156 or D 6045
See Note 1
Particulate contamination mg/L
Max 1.0
423
D 5452
See Note 2
Particulate, cumulative channel particle counts, ISO Code & Individual Channel Counts
Channel counts/ ISO code
565 or 577
D7619
See Note 2
≥ 4 μm(c)
Report / Max 19
See Note 3
≥ 6 μm(c)
Report / Max 17
≥ 14 μm(c)
Report / Max 14
≥ 21 μm(c)
Report
≥ 25 μm(c)
Report
≥ 30 μm(c)
Report / Max 13
COMPOSITION
See Note 4, 5
Total Acidity, mg KOH/g
Max 0.015
354
D 3242
Aromatics, % v/v.
Max 25.0
156
D 1319
OR Total Aromatics, % v/v
Max 26.5
436
D 6379
See Note 6
Sulphur, Total, % m/m
Max 0.30
336
D 1266 or D 2622
or D 4294 or D 5453
Sulphur, Mercaptan, % m/m
Max 0.0030
342
D 3227
OR Doctor Test
Negative
30
D 4952
See Note 7
Refinery Components at point of manufacture:
See Note 8
Non Hydroprocessed Components, %v/v
Report (incl. nil or 100%’)
Mildly Hydroprocessed Components, % v/v
Report (incl. nil or 100%’)
Severely Hydroprocessed Components, % v/v
Report (incl. nil or 100%’)
Synthetic Components, %v/v
Report (incl. ‘nil’ or ‘50%’)
See Note 4
INCIDENTAL MATERIALS
See Notes 9
VOLATILITY
Distillation
123
D86
or D7345., See Note 10
Initial Boiling Point, ºC
Report
Fuel Recovered
See Note 10
10% v/v at ºc
Max 205.0
Or IP 406 or D 2887
50% v/v at ºC
Report
see Note 11
90% v/v at ºC
Report
End Point, ºC
Max 300.0
Residue, % v/v
Max 1.5
Loss, % v/v
Max 1.5
Flash Point, ºC
Min 38.0
170 or 523
D 56 or D 3828
Or D93 (Procedure A) or IP534 / D7236
Density at 15ºC, kg/m³
775.0 min to 840.0 max
160 or 365
D 1298 or D 4052
FLUIDITY
Freezing Point, ºC
Max -47.0
16 or 435 or 528 or 529
D 2386 or D 5972 or D 7153 or D 7154
See Notes 12 and 13
Viscosity at -20ºC, mm2/s(cSt)
Max 8.000
71
D 445
D7945 or D7042, See Note 14
COMBUSTION
Specific Energy, net, MJ/kg
Min 42.80
12 or 355
D 3338 or D 4809
See Note 15
Smoke Point, mm
Min 25.0
598
D 1322
See Note 16
OR
Smoke Point, mm
Min 18.0
598
D 1322
AND Naphthalenes, % vol
Max 3.00
D 1840
CORROSION
Corrosion, Copper strip, classification (2 hours +/- 5 min. at 100 ºC +/- 1ºC)
Max 1
154
D 130
STABILITY
Thermal Stability
323
D 3241
See Note 17
Control temperature, ºC
Min 260
Filter Pressure Differential, mm Hg
Max 25
One of the following requirements shall be met:
(1) Annex B VTR
Less than 3, no Peacock or Abnormal colour deposits
(2) Annex C ITR or Annex D ETR, average over area of 2.5mm²
nm Max 85
CONTAMINANTS
Existent Gum, mg/100ml
Max 7
540
D 381
Microseparometer (MSEP), rating
D 3948
See Note 18
Fuel with Static Dissipator Additive
Min 70
OR
Fuel without Static Dissipator Additive
Min 85
CONDUCTIVITY
Electrical Conductivity, pS/m
50 min to 600 max
274
D 2624
See Note 19
LUBRICITY
BOCLE wear scar diameter, mm
Max 0.85
D 5001
See Note 20
ADDITIVES (Names and approval code from DEF STAN 91-091/12 should be quoted on quality certificates).
Antioxidant, mg/l in final batch (Optional)
Max 24.0
See Note 21 and Note 22
Metal Deactivator, mg/l (Optional) *
First Doping
Max 2.0
See Note 23
Cumulative concentration after field re-doping
Max 5.7
Static Dissipator, mg/l*
First Doping
Max 3.0
Cumulative concentration after field re-doping
Max 5.0
Antioxidants are still mandatory for synthetic fuels and shall be added prior to or during release from the designated manufacturing site of the ASTM D7566 component.
The types and concentrations of all additives used shall be shown on the original Certificates of Quality and on all other quality documents when they are added downstream of the point of manufacture. When additives are diluted (with hydrocarbon solvent only) to improve handling properties prior to addition, it is the concentration of active ingredient that shall be reported. See Annex A of DEF STAN 91-091 for detailed advice.
Fuel System Icing Inhibitor is not permitted unless agreed by all the participants in a joint system (see also Note 24)
See Note 25 about requirements for management of change in refineries.
Lubricity Improver Additive (LIA) additive may be added to the fuel without prior consent of the joint system participants (see also Note 20)
* When the original dosage of additives is unknown, it has to be assumed that first doping was applied at maximum dose rate.